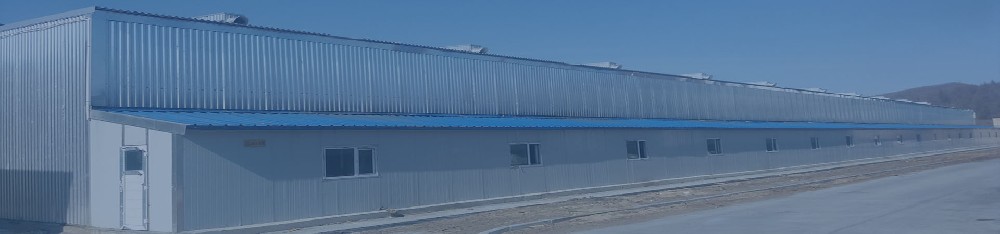
Product
Capacity m³ | Kiln Inner dimensions | Stack Dimensions | Number of Fans |
LDFJ-40 | 4.23×4.68×5.7 | 4.0×4.5×4.5 | 2 |
LDFJ-50 | 4.32×7.7×5.7 | 4.0×5.8×4.5 | 3 |
LDFJ-60 | 4.32×8.64×5.7 | 4.0×6.6×4.5 | 3 |
LDFJ-80 | 6.48×7.7×5.7 | 6.2×5.8×4.5 | 3 |
LDFJ-100 | 8.64×7.7×5.7 | 8.4×5.8×4.5 | 5 |
LDFJ-120 | 8.64×8.64×5.7 | 8.4×6.6×4.5 | 6 |
LDFJ-150 | 12.96×7.7×5.7 | 12.5×5.8×4.5 | 8 |
LDFJ-180 | 12.96×8.64×5.7 | 12.5×6.6×4.5 | 9 |
LDFJ-200 | 12.96×9.37×5.7 | 12.5×6.8×4.5 | 10 |
LDFJ-250 | 12.96×9.37×6.4 | 12.5×8.0×5.0 | 12 |
LDFJ-300 | 21.4×9.3×5.7 | 21.0×7.3×4.5 | 15 |
LDFJ-400 | 25.68×9.3×5.7 | 25.0×7.3×4.5 | 20 |
LDFJ-NS135 | 9.72×8.64×5.4 | 9.4×6.6×4.3 | 7 |
LDFJ-NS150 | 10.80×8.64×5.4 | 10.5×6.6×4.3 | 8 |
LDFJ-NS160 | 11.88×8.64×5.4 | 11.5×6.6×4.3 | 9 |
The wood drying kilns are available in track-loaded design or configured for loading by a forklift. With variable speed drives to reduce electrical consumption, high efficiency, adjustable pitch fans to optimize air flow and drying conditions, and accurate temperature and humidity control using advanced PID controller and refined in thousands of installations around the world.
The kiln is built in all aluminum kiln structure and kiln housing, construction for corrosion resistance and is installed on a concrete foundation. The construction consists of an aluminum inner wall and outer wall with fiber glass insulation in between. The multi-layer kiln structure can effectively balance expansion and shrinking stresses caused by temperature differences between the inside and the outside of the kiln while in operation. This ensures that the kiln stays properly sealed.
We adopt 150mm thickness profile to solve the insulation problem. In cold area like Siberia in Russia, where is -45 celsius degree, 2T boiler can support 8 of our 100M3 kilns.
We use 35x35mm big corrugated aluminum sheet for roof and outside panel of the housing,designed for cold area with heavy wind and snow. Slope roof design to prevent accumulation of rain or snow on the roof.
Wind and snow load is more than 200KG per square meter, suitable for resisting wind and snow in cold region.
“Hildebrand” wood dry kiln is equipped with high-temp motor and 800mm die-casting aluminum alloy axial fans.
Motors of insulation class H and protection grade IP55 can stably operate in high temperature and high humidity environment in a long-term.
Symmetrical blades ensure the consistency of air volume and air pressure in the two directions, so as to greatly guarantee the even wood moisture content. HDE Axial impellers, 100% reversible, optimum efficiency. Unique, easy pitch adjustment.
Schneider inverter (V.F.D) adjusts fan speed in different drying period when the air amount need changes, can save 30% electricity energy for hard wood. It is controlled by control system automatically.
Name: High temperature motor
Brand: Hildebrand
Rated voltage (380V)
Rated power (3.0KW)
Rated revolutions(1426 RPM)
Protection grade (IP55)
Max. working temp (115℃)
Name: Axial Propeller
Brand: Hildebrand
Material: Aluminum
Max air amount(30000m3/ h)
diameter:800mm
-100% Reversible
-Optimum Efficiency
-Unique, Easy Pitch Ajustment
Name: Frequency inverter (V.F.D)
Brand: Schneider
Power: 6KW-36KW
Energy saving:
Soft wood 20% electricity saving
Hard wood 30% electricity saving
Control directly by control system
“Hildebrand” heating and spraying system is composed of double metal heating coil, electric valve, electric spraying valve and other piping system. The extruded aluminum heating coil increase the heating surface to meet users’ production demand and prevent corrosion of sub-acidic environment inside the kiln, the stainless steel inner pipe can resist tube steam erosion, which maximally adapt to different water quality.
All the pipings and fittings are made of stainless steel to ensure long-term stability in sub-acid environment.
Harbin Hildebrand's focus has always been to support all Kiln owners and improve efficiency and productivity in lumber drying. Heat loss through venting is one of the most notable downfalls of a conventional kiln. With venting necessary to remove the excess moisture, you are stuck with considerable energy expenditure. This heat expenditure can significantly decrease your efficiency, increase your energy costs, and decrease degrade. Our Germany patented technology heat recovery system help recover energy lost during the drying process by transferring a large portion of the outgoing vented air's energy to the incoming air. This process utilizes energy that would otherwise be wasted, minimizing the need for “reheating” and reducing overall fuel consumption by a minimum of 11%.
International popular one-piece kiln door is in all aluminum suspension rail style. The whole kiln door is prefabricated with fiber glass insulation to thoroughly prevent thermal bridge effect and to optimize insulation performance. Particular high temperature resistant PVC insulation gasket strips are not aging in high temperature condition for a long time and will keep kiln door closely sealed. Door carriage adopts international popular style, stable movement, convenient to lift. Single wheel main door bracket is easy to operate, stable lifting and dropping, flexible slide, 13m main door can be handled by only one single person.
The aluminum intermediate ceiling is equipment under the fans, motors and heating coils, with the lowerable stack seal, the adjustable baffle, it can be adjusted with the stack sinking during the drying process to resist wind, a lasting solution free from leakage air with the lowest possible manipulation times for sealing off the stack from the intermediate ceiling. Optimum sealing-off of air for energy savings and and enhanced drying result.
Fiber glass insulation wool to prevent any thermal bridge effect and to optimize the insulation performance within the wall, roof and kiln main door. High density: 40kg/m3. The standard thickness of wool is 100mm, and 150mm in roof and door. Thickness can be added to 200mm for specific requirement.
The enclosed waterproof control room behind the back wall is included in the kiln structure, the control panels, computers and piping can be placed inside the control room.
LIGNOMAT Fully Automatic Control System, made in Germany and assembly in USA:
-All the products and technology from Lignomat are on basis of German HILDEBRAND drying technology.
-After over fifty years of improvement and renovation, Lignomat has received great support and reliance from European, North and South American, Southeastern Asia and African clients.
-Most advanced self-detect and alarm system.
-More than 5000 kilns are running safely and efficiently under control of Lignomat KCS.
-Accurate reading, easy operation and maintenance, online consultation and diagnosis, automatic generation of detailed analysis report nd chart.
-Fast drying time, less energy consumption, high lumber quality.
-Besides effective and reliable automatic wirebound systems, exclusive automatic digital wireless systems are available, no probe cable, no noise problem.
LIGNOMAT fully automatic control system combines the most advanced software and hardware equipment of Lignomat, unique design, less hardware, easy to operate.Fully automatic controller has modulating output for heat electric valve and vent motor to maximize the control of energy consumption and adjustment of the temperature and humidity in the dry kiln to save the drying cost, shorten the drying time.
The computer can display and store all the operation data, In-kiln temperature, MC and EMC of each MC probes for data statistics and technical analysis.
Host PC can be connected to internet, printer and other PC for remote control.
The wood waste produced in the machining process is collected and stocked in the silo.
The wood waste is transported by screw conveyer from excretive valve to the boiler.
The steam or hot water or hot oil or gas from the boiler is sent to the kilns for heating.
If you are interested in our products and want to know more details,please leave a message here,we will reply you as soon as we can.
Product Categories
new products
Copyright © 2024 Harbin Hildebrand Machinery CO.,ltd. All Rights Reserved. sitemap-xml sitemap-txt